Surface coating on containers, works much like how top coat of nail enamel works on nails. It makes way for the perfect shine, shimmer or gloss, and protect the substrate. It is the final stage for a package design to be put together. And when it comes to cosmetic packaging, the most dramatic jives of all is given out to the lipstick container! There is indeed much to realize about the shining and shimmering variations of surface handling technologies to make this tiny cartridge of beauty an exclusive design. This article explores and compares the aspects of these technologies, owing to factors like production process, time, cost, durability and of course, style, ultimately helping enterprises choose the ideals for lipstick packaging.
Lipstick containers serve as a beacon for make-up, and are by all means, truly iconic. An individual who perhaps has no sense or knowledge about cosmetics, knows the lipstick container for sure, just by the sight of the cylindrical format. The shine and gloss of the tubes has something to with its attractiveness, and overall brand value. Therefore surface handling is pivotal.
Types Of Surface Coatings Used For Cosmetic Packaging
Having the knowledge about different coatings is essential for cosmetic manufacturers, so that they are not just able to choose the right one, but can also be more adaptive to the changing market trends of design and functionality, owing to aspects of corrosion-resistance, waterproofing etc.
Plastic Injection (Extrusion)
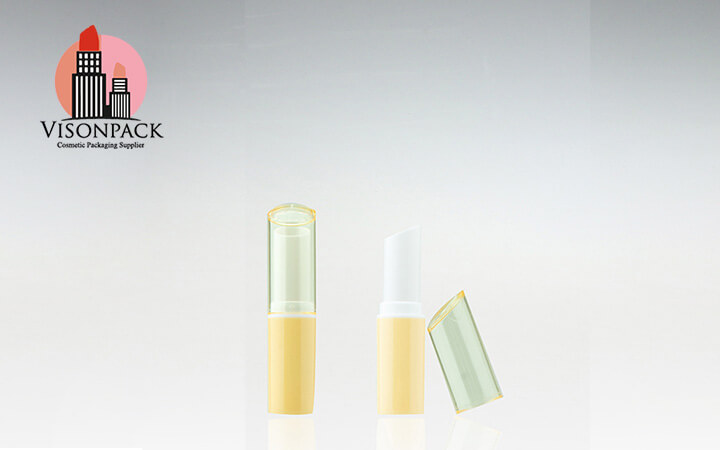
The polymer injection process involves the extrusion of molten polymers by injecting it into a mould, wherein it hardens when cooled, taking the shape of the mould. Injection molding is a common process for “laminating” lipstick packaging. Both thermosetting and thermoplastics are used at large for the purpose, at many instances other materials, like glass, wood fibres, and additives may be mixed into the compound in order to make it smoother and more durable. Once the parison has hardened, additional PVC coatings are applied to make it resistant to abrasion and galling or loose the lustre. Fibreglass reinforced resins are also used, that give them extraordinary sturdiness.
Pros
- 1.Easy process for coating tiny items like lipstick tubes and caps
- 2.Wide options for colorful containers
- 3.Takes minimum resources
Cons
- 1.Can be toxic for workers for the long run
- 2.Takes more time to dry
UV Coating
For UV coating, ultraviolet radiation is used to cure the substrates. It can achieve a multitude of design properties and features for polymeric containers, such as wear and scratch resistance, reduce glare and also prevent microbial buildup and fogging. UV coating is extensively used on lipstick containers, made of both metal and plastic, or mixed compound. The ease of application and quick production. The most significant aspect of UV coating is it’s high gloss finish, that can be used on small, detail oriented tubular containers with consistent all over coverage, and even spot coverage. It adds an instant shine of luxury to the packaging, and since they don’t use extreme heat to the point of thermolysis, the mechanism is safe for applying on thermoplastic containers, giving it a metallic finish at a reduced cost than actual metalization.
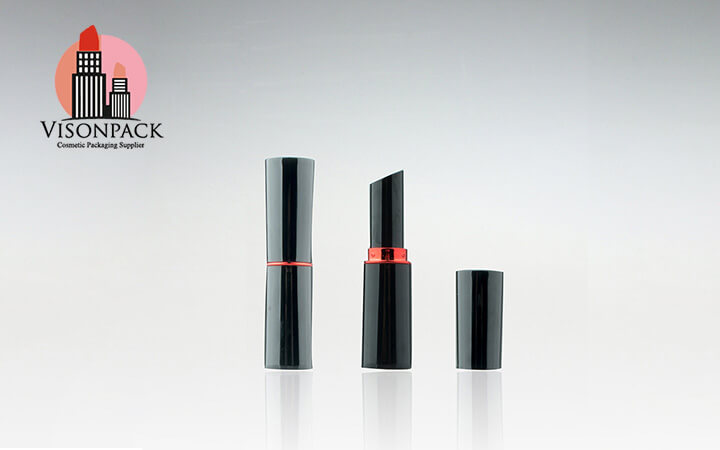
Pros
- 1.Eco-Friendly, and not harmful for the health of labors
- 2.High clarity, glossy finish
- 3.Prevents UV rays from heating up the product
Cons
- 1.Needs more resources
- 2.Can be expensive in the long run
Matte Coating
The amount of resins and binder agents are reduced to give matte coating a surface finish, that can come in variety of textures, like satin-like finish, eggshell finish, or just reduced gloss. This adds a minimalist, sophisticated look onto the cosmetic containers. It has excellent features of scratch-resistance and water-resistance. The most significant aspect of matte coating is that it can mask off wear marks or scratches to a large extent, and never show fingerprints. Therefore, these are quite ageless. This is a type of Aquous Coating, which uses water based compounds. They dry out quickly, and are cheap to make.
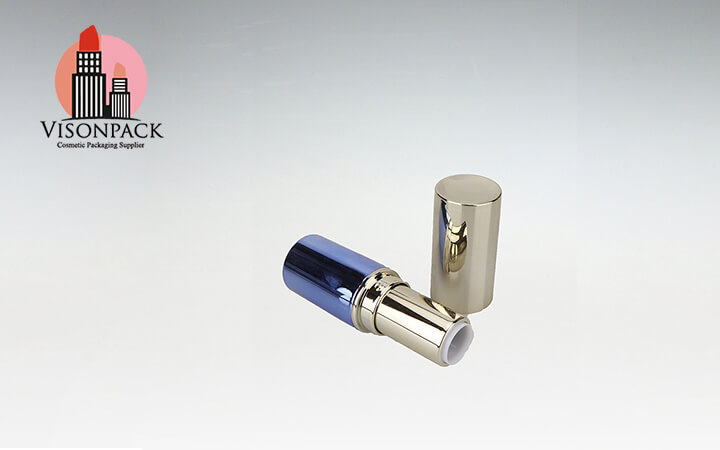
Pros
- 1.Provides a sophisticated, clean sheer
- 2.Resists scratches and moisture borne discoloration
- 3.Prevents handprints and stains
Cons
- 1.Can go unnoticed due to the lack of shine
Rubber Painting
Rubber coating comes as a singular paint-cum-coating format, serving a dual purpose. The composition of this surface handling technology is not new, which has gum plastic and paint mixed together, and may be applied on metallic or plastic container substrate making up for a high-performance sealant, delivering ample protection and style. The soft, velvety texture is both attractive and resistant to water and wear. The most beneficial aspect of rubber paint coating is that it can be directly painted or sprayed on the substrate, without needing heavy machinery. Whereas, the paint is not so well tolerant to go with scratches and extreme heat, and may peel off over time.
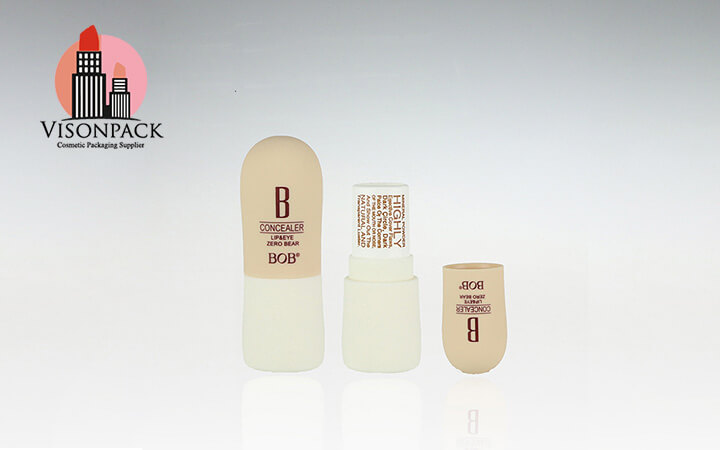
Pros
- 1.Prevents metallic containers from getting heated up due to heat
- 2.Provides a suede like texture
- 3.Is Water-resistant
Cons
- 1.Can’t mask off scratches so well
- 2.Can peel off or get sticky at high temperature
Metalization or Metalizing
Metalization is the process of layering metallic substance, mainly alloys, or chromic acid to coat over the substrate. This can produce a glossy exterior, and is largely resistant to scratches or cracking if slipped off hands. Physical Vapour Deposition or PVD coating is the mostly used technology for Metalization that layers a thin metallic film. This is a significant way for plating plastic containers, giving it a metallic finish.
Pros
- 1.Completely seamless finish
- 2.Prevents scratches and abrasion
- 3.Cost effective in the long run
Cons
- 1.Have low tolerance to heat or cold
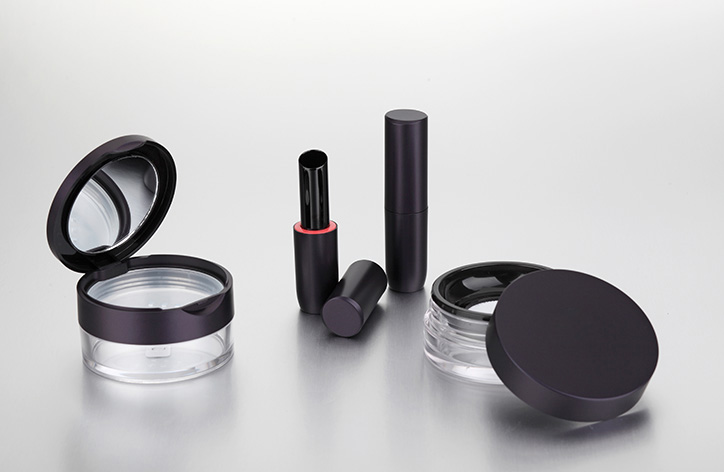
Conclusion — Choose The Right Surface Handling Technology For Lipsticks
The format of lipsticks is that it is largely carried around, and a protective packaging, requires to have heavy duty insulation properties, that will prevent the wax and oil based solid from melting. Other things to be careful when choosing the right surface handling technology is be adherent to the guidelines and regulations levied by the Government of your country, ranging from material grades and standardization ratings. So this area needs to be fully transparent, when dealing with a packaging manufacturer, and should share the standards of materials they are using.